Intel Sees 275% Increase in Reuse, Recovery
Kathleen Fiehrer, materials engineer at Intel, discusses the company’s sustainability success and its commitment to recovering resources.
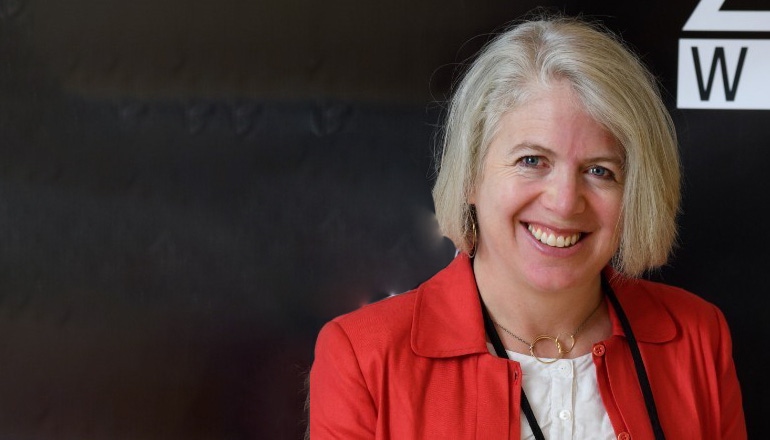
Since 1994, Santa Clara, Calif.-based Intel Corp., a leader in the semiconductor industry, has maintained a focus on sustainability. In just the last three years, the company has increased the reuse and recovery of its manufacturing waste by 275 percent.
“Intel has a long-standing commitment to environmental leadership, which has shaped our ongoing dedication to sustainability and continues to help our leaders plan for the future,” says Kathleen Fiehrer, materials engineer at Intel. “We continually invest in conservation projects and set companywide environmental targets, seeking to drive reductions in greenhouse gas emissions, energy use, water use and waste generation.”
Fiehrer, whose career with Intel spans the past 20 years, has been instrumental in the company’s environmentally conscious efforts.
“We are currently working to develop our 2030 goals, which will largely shape the trajectory of our sustainability plan,” says Fiehrer. “We are approaching the next decade with a global mindset and looking to demonstrate how our products, services and programs are part of the solution to global environmental challenges.”
Waste360 recently sat down with Fiehrer to discuss her role in Intel’s sustainability success and the company’s commitment to recovering resources.
Waste360: Please describe your role as materials engineer in the supply chain organization.
Kathleen Fiehrer: I primarily focus on developing and implementing disposal strategies for Intel’s global manufacturing waste in partnership with our suppliers while ensuring alignment with larger company and industry strategies.
Not all options are implemented due to technical feasibility, logistics or cost, but we continue to identify new options to achieve a circular economy for our waste. From a day-to-day operations point of view, I also ensure business continuity within the supply chain to ensure we continue to operate 24/7/365.
Waste360: How have you been instrumental in the company’s efforts to lead with an environmentally conscious mindset?
Kathleen Fiehrer: Over the last two decades at Intel, I have had the opportunity to work in a variety of sustainability positions, providing the opportunity to grow professionally as well as to influence Intel’s environmental efforts.
Initially, I worked as a facilities engineer installing and optimizing waste treatment systems in the early 2000s to meet or exceed our environmental targets. However, when I joined the supply chain organization in 2012, I was able to directly partner with our supply chain to drive sustainable disposal practices throughout the corporation.
In the last seven years, Intel has been on a journey to achieve its goal of a 90 percent non-hazardous recycling rate and zero hazardous waste to landfill by 2020.
Waste360: How has the company’s sustainability approach changed over the last 20 years?
Kathleen Fiehrer: Through increased awareness and new technologies, we casted a wider net and raised the importance of sustainability across business units. This heightened focus established a culture of sustainability throughout our global operations and created a workforce that prioritizes discussions of environmental impact in decision-making. We have tied compensation to the achievement of sustainability goals for years.
In addition, we adopted an increasingly data-driven approach to sustainability, setting measurable and transparent goals in order to hold ourselves accountable to progress. While there is always room for growth, the last 20 years have shown consistent forward momentum in the realm of environmental impact with Intel taking an increasingly holistic approach to sustainability throughout our business operations.
What has not changed in the last 20 years, and may prove most significant, is the value our efforts have brought to our company, customers and the communities in which we operate.
Waste360: What is Intel’s commitment to recovering and regenerating resources from semiconductor manufacturing?
Kathleen Fiehrer: As a global leader in manufacturing, Intel is cognizant of our environmental impact and deeply committed to reducing our footprint through a transparent, data-driven approach to sustainability. Intel has an established history, spanning nearly 30 years, of voluntarily disclosing key environmental data.
We share information on waste generation and reuse efforts and regularly set new goals in our path to greater sustainability. This approach has led to a solid recycling rate of more than 90 percent, up from 25 percent in the mid-1990s, with zero impact on manufacturing output.
Today, Intel’s commitments to semiconductor manufacturing waste are largely focused on shifting from traditional disposal methods at the bottom of the waste disposal hierarchy, such as incineration and landfill, to disposal methods near the top of the hierarchy, such as recovery and reuse of materials.
By focusing on recovery and reuse, we reduce our environmental footprint, bolster the circular economy and identify new opportunities to address manufacturing waste stream disposal. We are on track to achieve our goal of a 90 percent non-hazardous recycling rate and zero hazardous waste to landfill by 2020.
Waste360: What steps is Intel taking to honor this commitment?
Kathleen Fiehrer: Intel’s commitment to recovering and regenerating resources in our manufacturing operations is built upon a foundation of transparency, governance and ethics. We released our first voluntary environmental report in 1994 and have since been building upon these commitments.
In 2018, Intel took the next step in advancing our reporting by further integrating corporate responsibility data into the Annual Report/10K and Proxy Statement.
Employee engagement is key to meeting our environmental goals. Since 2008, we have linked a portion of each employee’s compensation to achieving environmental sustainability metrics.
By setting companywide environmental targets, involving employees, investors and customers in the goal development process and benchmarking our progress annually in our Corporate Responsibility Report, we take a data-driven and measurable approach to meeting our goals.
Waste360: How did the company increase the reuse and recovery of its manufacturing waste by 275 percent in the last three years?
Kathleen Fiehrer: Since 2015, we have focused on new disposal methods to minimize incineration and the use of landfills, ultimately resulting in a 275 percent increase in reuse and recovery. We partnered with our waste disposal suppliers to identify and implement alternative disposal methods that would move our disposal methodology up the waste hierarchy.
The methods include direct reuse, recovery, recycling, fuel blending and treatment to neutralize materials for greater disposal, only relying on safe incineration and Intel-approved landfills as a final resort.
Over the course of three years, we have increased our priority disposal method of direct reuse by 11 percent. The combination of direct reuse of materials in secondary industry and the recovery of materials for chemical feedstock in other industries accounts for more than 50 percent of Intel’s disposal of manufacturing waste.
Alongside this increase, landfill use has decreased 50 percent since 2015 and incineration ranks as the third lowest disposal method, with only 13 percent of manufacturing waste being incinerated in 2018. Some of the waste streams Intel has moved into recovery and reuse disposal are ammonium sulfate, fluoride byproducts, lithography-related solvents, metal plating waste, specialty base cleaners and spent sulfuric acid.
Looking to the future, as our semiconductor manufacturing becomes more complex, we will continue to identify new disposal options to upcycle our waste.
Waste360: How have you partnered with suppliers to move manufacturing waste up the “waste hierarchy” toward reuse and recovery?
Kathleen Fiehrer: Our waste management suppliers play an essential role in our reuse and recovery efforts, aiding Intel in identifying potential opportunities on a global scale, while also providing the necessary expertise to drive our vision for sustainable manufacturing forward.
For example, through a collaborative effort with onsite and third-party waste management partners, we were able to largely upscale reuse and recovery efforts at the Ireland campus, cutting waste management costs by 50 percent since 2014. As a result of these efforts, we expect more than 80 percent of the site’s manufacturing waste to be reused or recovered by the end of this year.
We worked alongside waste management partners to drive these results in a variety of ways, most notably by:
Moving calcium fluoride waste from landfill to an ingredient component in cement product manufacturing.
The distillation and recovery of a lithography solvent for resale.
Recovering semi-precious metals for metal recovery rather than sludge generation.
Converting our spent sulfuric acid and ammonium sulfate to inputs for fertilizer manufacturing.
We are proud of the suppliers we have chosen to partner with and continually do our due diligence to ensure they are aligned with our 12 environmental, labor, ethics, health and safety and diversity and inclusion expectations. Our latest Corporate Responsibility Report has robust data on the ways in which we have partnered with our suppliers to increase sustainability across business units.
About the Author(s)
You May Also Like