Plastic Odyssey Embarks on Transcontinental Expedition to Showcase Micro Recycling Factories
Simon Bernard, Plastic Odyssey CEO, used to be a merchant Navy officer, sailing from Morocco to Senegal. In this former life he joined an expedition working on low-tech solutions to turn seawater into fresh water and to grow food so people in nearby coastal communities would have resources to help sustain themselves. During long hours working offshore he came to realize there were tremendous volumes of plastic floating in the ocean.
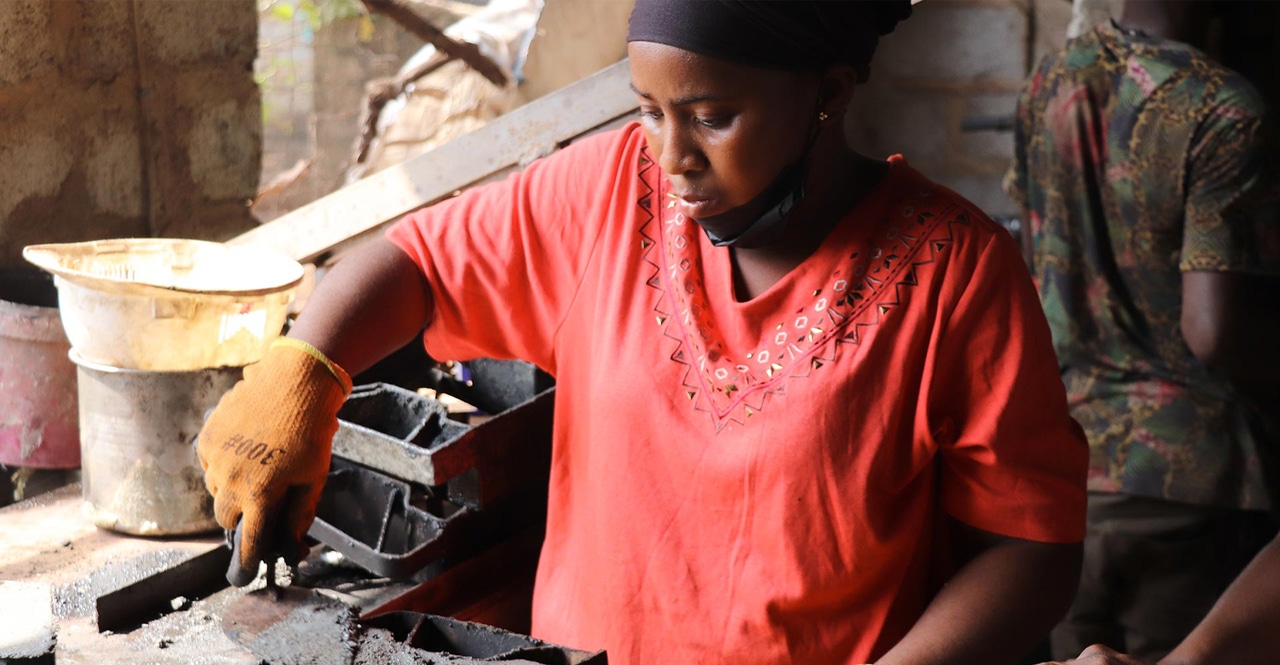
Simon Bernard, Plastic Odyssey CEO, used to be a merchant Navy officer, sailing from Morocco to Senegal. In this former life he joined an expedition working on low-tech solutions to turn seawater into fresh water and to grow food so people in nearby coastal communities would have resources to help sustain themselves.
During long hours working offshore he came to realize there were tremendous volumes of plastic floating in the ocean. He thought if there was as simple and economic a way to recycle plastic as to process sea-water, locals in these developing countries could take on plastic trash to help solve the pollution problem. At the same time, they could make a living.
Fast forward to 2017, which is when Bernard launched Plastic Odyssey, a social enterprise aiming to develop a global network of recycling entrepreneurs and to help build plastics recycling infrastructure, though the plan is to eventually work to cut plastic use, perceived by the team as a longer-term solution.
Based in France, the company has set its sights on Africa, Asia, and South America. Its early work has included beach cleanups and trying to better understand the plastic waste-related problems in those regions to determine best pathways to tackle those problems. But the business model has since evolved.
The team is beginning to offer containerized plastic recycling machines in these targeted coastal communities. These “micro factories,” as Bernard calls them, run about $50,000 to $100,000. The company is training entrepreneurs on how to set up, operate, and maintain them.
A Plastic Odyssey team will set sail in October 2022 on an expedition to 30 countries in Africa, South America, Asia, and the Pacific, where it will showcase the equipment that will be installed on board so locals can see how it works. There are different packages, with capabilities such as shredding, washing, drying, and extruding plastic.
“Entrepreneurs at the sites we visit can test it out. We will try and inspire them to replicate solutions. This is how it works. And you can translate to your own context,” says Jean-Baptiste Grassin, Plastic Odyssey Global Recycling project coordinator.
“People mainly from Africa and Asia are contacting us because they have an idea to address plastic waste, or they already have a small company. But they lack needed training and other resources,” Bernard says, which is why support will be part of the package.
Those who already run operations typically work a very physical job, without adapted equipment and often under extreme conditions, sometimes in direct contact with fire and intense heat rising up from plastic melting pots that increase the risk of accidents.
But while their resources are nonexistent, or inadequate at best, high-tech systems are not necessary to run an efficient, safe, and prosperous operation in these developing regions, according to Bernard. In fact, highly sophisticated infrastructure would not work, he says. There are few to no companies to repair or maintain equipment, and spare parts are hard to come by. There is typically no electricity and water at these remote sites.
“But you have people who will do manual work who just need basic equipment and training to recycle plastic. That’s where we need to act, and that’s where we see opportunity to help,” Bernard says.
Getting a return on investment –both for Plastic Odyssey and prospective customers—requires having a working business model. With that thought in mind the strategy is to clusterize solutions in subregions; relatively small-scale operations that are easy to build and replicate.
“It doesn’t require a million-dollar set up that involves many stakeholders. Yet you can still have significant impact; you can recover hundreds of tons per year. And you can be profitable because it makes sense economically at this scale,” Grassin says.
Plastic Odyssey plans to secure funding to advance the model through local organizations and corporations. One ambition is to build and test factories through a joint venture with corporations.
Grassin sees shared ownership as an opportunity to remain hands on and to scale quickly.
“We would work with the same corporations to set up in other countries, and adjust the model depending on the markets there,” he says.
So far two projects are locked in, and plans are to launch five more micro factories per year over the next three years, Bernard says, while discussions are ongoing with other prospects interested in setting up their own operations.
Mariam Keita, who owns Binedou Global Service in the commune of Coyah in Guinea, will become the first taker. She has been making plastic paving blocks through a labor-intensive, manual process exposing her to high heat and toxic fumes. She cuts the plastic by hand, melts and stirs it in a pot over a wood-burning fire; mixes it with sand; scoops the mixture into molds; and waits for it to dry. She can make 200 paving blocks a day, tops.
With her new machine, she will be able to make 500 blocks per day through a semi-industrial process whereby a shredder reduces the plastic waste into flakes, which go to a temperature-controlled extruder where they are transformed with mixed-in sand into a homogenous melted paste, then automatically transferred to a hydraulic press to be precisely shaped.
“Today, we are not able to satisfy the demand or to deliver orders on time. The evolution towards this production process will allow us to absorb this demand. It will allow a greater capacity, better quality of the final products, and much better working conditions,” Keita told Waste360 through a translator.
Plastic Odyssey provided her funds to get the project off the ground and connected her with government officials in her region who granted her about 2.5 acres of land to set up.
Keita will make a product that does not yet exist in Guinea, she says, adding, “Guinea is one of the dirtiest countries in the world, and I want to transform enough plastic waste to clean it as best as possible.
Our dream is also to make other products, like tables and benches for schools. I dream to innovate every day to be closer to the needs of my country.”
Plastic Odyssey’s ambition is to get a grasp on consumption and disposal habits in the countries it visits, and to ultimately do further research to figure out how to curb plastic use.
“Simply installing micro factories is not enough. We will recycle waste that is already there to act urgently. But changing habits and finding alternatives to plastic use is where we plan to go next,” Bernard says.
About the Author
You May Also Like